
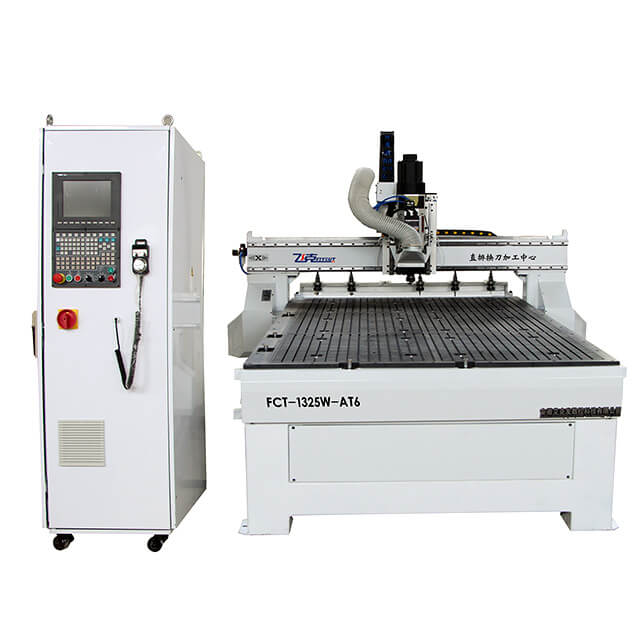
Of course, fly cutting, as with common cutting, can bring the risk of collision, so this must be used in conjunction with intelligent path optimization and crash avoidance. Fly cutting will reduce cutting time dramatically and, if your CAM system is capable enough, can actually be used to cut the whole nest when lead-ins/lead-outs are not necessary. It will continue to ‘snake’ through all horizontal cuts until it reaches the bottom row, after which it will move onto the vertical cuts. Then, as it travels off the grid to the next line of cuts, a radius can be placed on the path, meaning that the laser does not have to stop the head movement completely in order to change direction, reducing machine wear. In other words, if you have a grid of, say, 10 x 10 rectangular holes, the beam might start top left and move the head say horizontally, cutting the top-most part of the holes by rapidly switching the beam on and off as it travels between them.
FLYCUT MACHINING SOFTWARE
Also, this technique is only suitable for thinner materials.įly cutting works by software analyzing the nest and identifying grids and lines of holes and then splitting the cutting into separate short line or arc segments that lie on the same line or circle. This is only relevant for users of machines that will support this functionality. If your components often contain arrays of holes such as air vents then fly cutting, also referred to as grid cutting can drastically reduce cutting time. However, when performing common cutting there are other considerations to take into account, such as sheet stability on machines with fixed head and intelligent cutting of notches at the adjacent component edges. Not only can this save material and consumables, but it can also significantly reduce the machine runtime. This is the process of eliminating the skeleton between parts, separating them instead with a single cut. Let’s start appropriately with one of the most common ways to improve efficiency – common cutting. It is during these two processes that advanced technologies can be applied that can reduce runtime and wear on the machine as well as improving the quality of the finished part. Next, it needs to go through the CAM process, with cutting technology applied based on the CNC machine to be used, followed by the creation of a nest of one or more components. Either way, you may not necessarily be getting the best performance out of your machine.Ī component starts life in CAD – perhaps either as a single entity or part of a more complex assembly. Martin Bailey, General Manager of JETCAM explains techniques that can squeeze more performance out of your CNC laser.ĬADCAM/nesting software may either have been supplied alongside your machine or you may have sourced a system to drive multiple brands and cutting types. Yet often companies will overlook the relatively inexpensive cost of appropriate CAM and nesting software that could get significantly better performance out of their investment. See a demonstration on YouTube at For more information, contact Paul Carter, Plastics International, 7600 Anagram Dr.The purchase of a new fiber laser is not an insignificant one.

Plastic sheets can be flycut to finishing thickness requirements before being saw cut to smaller parts enabling machinists to eliminate multiple steps and set-ups when the surface thickness of parts is already planed to size. The flycutter is not used on glass filled materials or phenolics. Flycutting provides a close tolerance finish on plastics like Delrin® -acetals, UHMW, nylon, Teflon®, Ultem®, PEEK, ABS, polysulfone, Kynar® - PVDF, PET, Polyolefins and more.

Plastic sheets are typically flycut on both sides to balance properties and minimize warpage. 125” to 3” thick with a finish tolerance of +/. Maximum sheet capacity for the flycutter is 36” x 72” and sheet thickness from. Their vacuum operated flycutting machine for close tolerance horizontal planing of plastic sheets has specialized cutters on both ends of a 36” wingspan arms for maximum sheet widths. Flycutting is ideal for customers who have special sheet thickness requirements including metric thickness and resurfacing needs. Plastics International offers flycutting of plastic sheets for special thickness requirements as a finishing option beyond their CNC saw cutting services. The Plastics Distributor and Fabricator - Your Industry Magazine
